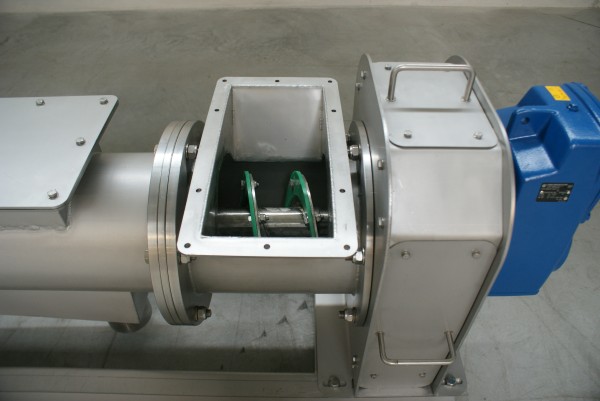
Modern device for dewatering and compressing solid waste from grates and sieves. It consists of a drum in a pipe with a screw that transports and compresses waste, and water flows out through holes. The compressed waste is pushed out, and used in many industries.
Modern equipment for dewatering and volumetric compression of solid waste separated on grids and sieves (‘screens’).
The design consists of a drum hidden in a pipe with a screw moving inside the drum. Waste falls through the inlet hole onto the screw, which transports it in the body to the drum. The waste transported by the screw meets resistance from the disc mounted at the outlet of the drum. Water squeezed out of the waste flows through holes in the drum, and the compressed waste is pushed out of the press. The intelligent design allows for use in almost all industries.
Pneumatic cylinders provide strong pressure which is also gentle. The operator can adjust the pressure force to achieve the best dewatering effect, without fear of damaging the disc. Hard objects that are not subject to compression will not damage the mechanism, because the cylinders will immediately retract to let them through. The press dewaters waste strongly without jamming on objects that could damage mechanical devices.
Maintenance and cleaning of the press is easy, because the structure has been designed in a way that allows direct access to parts exposed to the risk of clogging. All key construction points are protected against water. The entire device can be conveniently washed using high-pressure washers.
Mechanical separation, i.e. separating solid elements from the wastewater stream
Most industrial wastewater streams contain solids that must be removed before wastewater reaches the treatment plant equipment. Removal of solids is necessary to protect pumps, mixers, sensors and other system components from blocking or even damage. In EMI installations, we use two stages of mechanical pre-treatment: coarse and fine. Coarse pre-treatment removes the largest elements, with a cross-section above 20 mm, and is carried out at the inlet to the first pumping station, before wastewater comes into contact with any pump. Coarse separation devices include vertical screens, basket screens and step/hook screens. The purpose of fine mechanical pre-treatment is to further remove solids, with their cross-section dropping below 3 mm, most often to 1 mm, although in some cases it is appropriate to use even smaller cross-sections (up to 0.25 mm). At this stage, rundown and rotary screens are used. The latter type of screen is used in a system with external or internal inflow. Mechanical pre-treatment involves very low costs, mainly resulting from the consumption of water rinsing the screens. No reagents are used, and energy consumption is minimal. Mechanically pre-treated wastewater is suitable for further treatment by physico-chemical and biological means.
Devices for removing water from sediment by pressing, squeezing and other mechanical methods.
Dewatering of sludge generated during the treatment of industrial wastewater is a key process aimed at reducing the volume of sludge and improving its properties for further processing or disposal. This process involves removing as much water as possible from sludge, which is achieved using various methods, such as centrifuges, filter presses or vacuum dewatering. The main goal of dewatering is to reduce the mass and volume of sludge, which translates into lower transport and storage costs. Dewatered sludge also has better mechanical properties, which facilitates its further processing, such as composting, incineration or biogas production. Additionally, reducing the water content in sludge minimizes the risk of leaks and environmental pollution. The dewatering process can also increase the efficiency of further treatment stages, for example by improving the conditions for anaerobic digestion. Thanks to sludge dewatering, the process of treating industrial wastewater becomes more economical and environmentally friendly.
EMI offers specialized containers with built-in equipment for the implementation of any industrial wastewater treatment processes.
EMI has developed modular container systems in a marine version and designed to be connected into larger systems. The containers we offer have been designed from the ground up to operate in the harsh conditions of industrial sewage treatment plants. The interiors are lined with 100% stainless steel, have heating, ventilation, health and safety devices and individually configured technological equipment. The use of container construction allows for the shortest possible project implementation time. The entire installation is prefabricated in the EMI production plant and is delivered ready for start-up immediately after connection on site (in some cases preparatory works are required, such as tanks and underground networks, ground hardening, etc.). EMI's offer also includes tanks in containers that can perform averaging, storage and even become biological reactors.