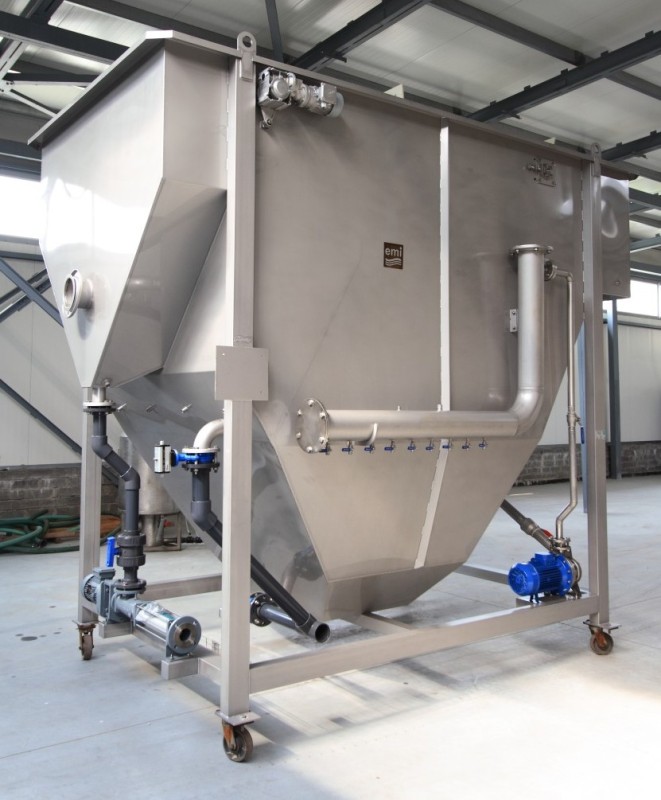
EMI flotation units with internal partitions reduce the size of the units without losing efficiency. Removable, stainless steel lamella packs allow easy cleaning without a crane, maintaining high efficiency. Ideal for wastewater with limited suspended solids.
A special type of flotation unit equipped with internal partition walls that allow for a significant reduction in the size of larger units while maintaining their cleaning efficiency.
The lamella packs in EMI units are made of stainless steel for durability and offer the possibility of removing them for cleaning one by one, which means that maintenance does not require a crane and can thoroughly clean the inserts, so that the efficiency of the unit remains at the same level.
Lamella packs are most suitable for wastewater with a limited amount of suspended solids.
Flotation systems require stable operating conditions, in particular a constant inflow of wastewater. In the systems offered by EMI, pumps with inverters controlled based on flowmeter readings are used. Thanks to this, the amount of wastewater flowing into the flotation unit is constant over time and does not depend on the filling level of the retention tank or the inflow of raw wastewater.
Depending on the characteristics of the wastewater, EMI flotation units can be equipped with lamella packs, which significantly reduce the dimensions at the cost of a slight increase in the height of the unit. All lamella plates are made of stainless steel to ensure reliability. Service teams will appreciate the ability to remove individual plates for cleaning and inspection.
The change in the hydration of the flotation sludge in EMI units can be done with the touch of a finger on the control panel. Intelligent automation takes care of setting the correct operating mode for the scraper.
The saturation control system used in EMI flotation units allows for precise regulation of pressure and air flow parameters. Water for air saturation is taken from the treated water and supplied by a separate pump, which prevents the unfavorable phenomenon of cavitation. Air is dissolved in the water in an L-shaped pipe. Saturated water is introduced into the flotation chamber through many nozzles placed in carefully selected places.
Each flotation unit supplied by EMI is designed individually. The starting point for the design is standard solutions, but our designers can take into account special customer requirements, e.g. dimensions or special additional functions.
EMI offers a unique solution for applications where it is not possible to ensure a constant inflow of sewage over time. Each flotation unit can be equipped with an intelligent flow control system. A change in the set flow on the control panel is automatically translated into new settings for pumps and other devices so that optimal operating conditions of the system are maintained. The system will take care of controlling sewage pumps, chemical dosing pumps, and even maintain an unchanged level of water in the flotation unit. EMI DAF units may also monitor the quality of wastewater and automatically adjust chemicals dosage to make sure that you use only as little as is required to get the best treatment result. Both overdosing and underdosing may become history if you opt for EMI DAF.
In cases characterized by a large amount of bottom sediment, standard solutions based on pneumatic gate valves may be insufficient. EMI then recommends the use of a screw conveyor responsible for collecting the sediment at one point at the bottom of the flotation unit, from where it is effectively removed.
In response to the diverse requirements of customers, EMI offers a wide range of materials from which flotation units can be made. From standard AISI304 stainless steel to specialist AISI904 steel. We also offer devices designed for work in special conditions (including ATEX), container solutions, etc. Hundreds of projects prove that EMI can offer a flotation unit for almost every application.
Each DAF unit can be equipped with a light cover that reduces evaporation and odor spread. Each cover is adapted to connect to the ventilation system. We also made sure that the service will have easy access to key elements.
Flotation is the most effective method of removing contaminants such as fats, suspensions, and petroleum substances.
Flotation is the most effective method of removing contaminants such as fats, suspensions, oil-derived substances and other undissolved substances found in industrial wastewater. The separation of these contaminants takes place in chemical processes using coagulants and flocculants (polymers). After separation, separation takes place using a water-air mixture in the flotation chamber. The resulting sludge is discharged outside the system and possibly dewatered before being disposed of, e.g. in a biogas plant.
EMI offers specialized containers with built-in equipment for the implementation of any industrial wastewater treatment processes.
EMI has developed modular container systems in a marine version and designed to be connected into larger systems. The containers we offer have been designed from the ground up to operate in the harsh conditions of industrial sewage treatment plants. The interiors are lined with 100% stainless steel, have heating, ventilation, health and safety devices and individually configured technological equipment. The use of container construction allows for the shortest possible project implementation time. The entire installation is prefabricated in the EMI production plant and is delivered ready for start-up immediately after connection on site (in some cases preparatory works are required, such as tanks and underground networks, ground hardening, etc.). EMI's offer also includes tanks in containers that can perform averaging, storage and even become biological reactors.